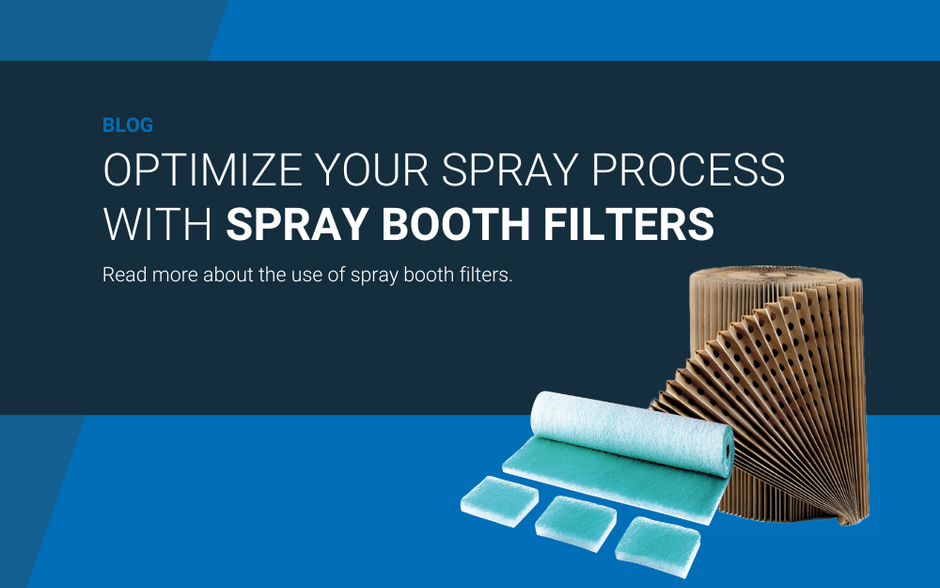
Spray booth filters are essential in any environment where paint or coatings are applied. The filters not only ensure a clean and safe working environment, but they also improve the quality of the finished products and protect the environment and the technical installation of your spray booth. In this blog, we dive deeper into the proper use of spray booth filters to optimize the working environment and improve production processes.
Why are spray booth filters important?
Spray booth filters play a crucial role in maintaining a controlled environment during the painting or coating process. The spray booth filters prevent paint particles from settling on surfaces, which can cause imperfections in the final product. They also ensure that harmful substances, such as dust particles, paint mist, volatile organic compounds (VOCs), and other harmful fumes, do not enter the outside air, reducing the negative impact on the environment.
Where are spray booth filters applied?
Although traditional automotive spray shops are often the first association, spray booth filters are used in many different industries. Examples include:
Furniture spray shops, where spray booth filters are used for high-quality finishes of furniture.
Aviation maintenance, where strict controls on paint and coating applications are required.
Yacht building, where spray booth filters are used for the perfect finish of ship surfaces.
Industrial coatings, in production environments where metals and other materials are coated using spray booth filters.
Metalworking companies, where spray booth filters are used where paint and coatings are essential for protection and aesthetics.
Paint lines in production halls, for consistency and quality in mass production.
Art world, for applying paint to large canvases in a dust-free environment.
Additionally, filters are also used in drying chambers to purify the air and remove dust particles, contributing to a smooth and even drying of sprayed materials. In short, spray booth filters are used wherever a clean, controlled environment is required for applying paint or coatings.
What role do spray booth filters play?
The correct filters in spray booths are important for a healthy work environment. When using products that contain harmful substances, these substances are released into the working environment or particles settle on the freshly applied paint, leading to undesirable results. Using the right filters prevents this and ensures clean recirculating air, which benefits the health of workers.
Common types of spray booth filters
There is a wide range of spray booth filters used across different market segments, including:
Pre-filters are used to filter out the largest dust and dirt particles from the air before they enter the spray booth. Their function is to protect subsequent filters, such as fiberglass bag filters, and extend their lifespan.
Ceiling filters are located in the ceiling of the spray booth and ensure that incoming air is free of dust before it enters the booth.
Wall filters are located on the sides of the spray booth and capture paint mist and overspray, preventing the mist from spreading and settling on surfaces.
Floor filters are used to capture paint mist and overspray that is drawn into the booth from the floor. These filters are installed on the floor of the spray booth.
Exhaust filters (Nafilter) are located in the exhaust system after the replacement filter and are intended to capture any particles before the air is expelled or recirculated.
On what criteria are spray booth filters selected?
When selecting spray booth filters, several factors must be taken into account to ensure optimal performance:
Type of Spray Process
Different spraying processes require specific types of filters to work effectively. For example, wet paint processes have different filter needs than powder coating processes. For primer and industrial paints, it is often better to use a Sepapaint filter with a Paintstop mat behind it. These types of paints are heavier, and a standard Paintstop mat clogs faster, making a Sepapaint filter more effective. For 2K automotive paints, it is often best to use a Paintstop mat with a synthetic filter mat behind it to protect the rest of the filter stages and installation from potential overspray.
Level of Contamination
The degree of contamination in the air determines which type of filter is most suitable. High contamination levels require stronger filters with a higher capacity.
Size and Capacity of the Spray Booths
The size of the spray booth and the amount of air that needs to be filtered play an important role in selecting the filter.
Regulations and Standards
Filters must comply with local and international regulations and standards for air quality and safety.
Ease of Maintenance
Filters should be easy to replace and maintain to minimize downtime and maximize efficiency.
More information or advice about your spray booth filters?
Interfilter not only looks at your current situation but also potential improvements such as longer service life, better filtration, and the possibility of recirculation to save on energy costs. This ensures that your filters not only meet current standards but also progress in efficiency and sustainability. Would you like to know more about spray booth filters or need advice? Feel free to contact me at 0181 32 08 88 or via email at info@interfilter.nl.