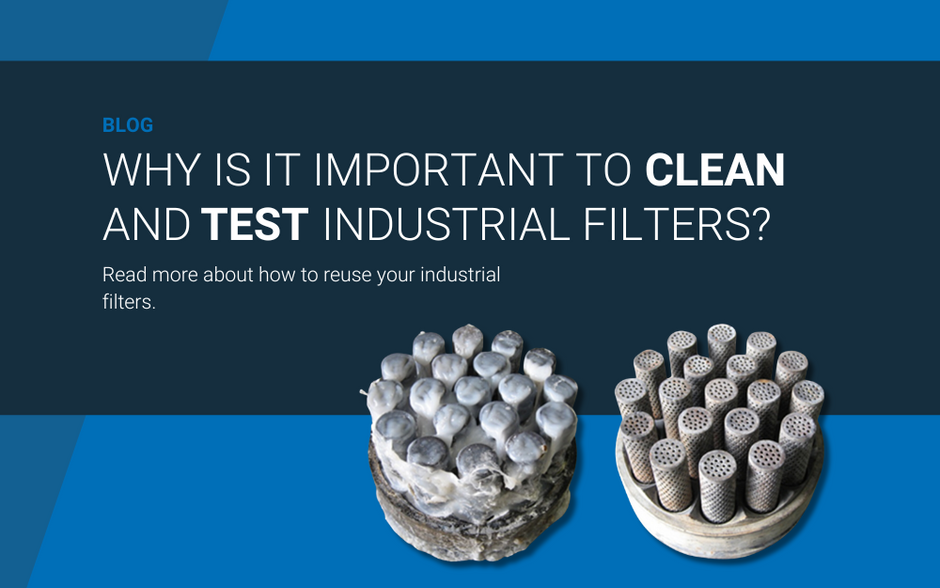
Cleaning and Reusing Industrial Filters
To ensure that both you and we can contribute to waste reduction, we now also offer the option to have various industrial filters cleaned. Interfilter Group is happy to work with you to find the most optimal cleaning process. Cleaning filters provides the following benefits:
- Makes filters more circular.
- Sustainable, as it reduces waste and CO2 emissions.
- Improves processes, resulting in significant cost savings.
- Ensures you always have a complete set of fully functional filters in your process.
- Gives you insight into the actual performance of your filters.
Which Filters Can Interfilter Group Clean for You?
Not all filters can be cleaned without compromising specifications. Interfilter can clean metal filters, filter plates, polymer filters, as well as process parts. Below are some examples.
What Does the Filter Cleaning Process Look Like?
Our filter cleaning process follows these steps:
Receiving Filters
Upon receiving the filters, a visual inspection is conducted to check for any damage. If any damage is detected, we will inform you and can immediately replace the filter with a new one.
Filter Treatment
Each type of contamination and material requires a specific cleaning technique, so we use various methods: thermal cleaning, ultrasonic cleaning, chemical cleaning, glycol cleaning, and high and low-pressure water cleaning. We always strive to use the least harmful method for both your materials and the environment while achieving the best results.
Cleaning Techniques Available
During the cleaning process, we may use different techniques and equipment, such as leaf filter cleaning, a semi-automatic wash station, small oxygen ovens, low-oxygen ovens, ultrasonic installations, rinsing control equipment, and a TEG installation.
We employ multiple techniques, with chemical cleaning being the oldest and most comprehensive method. Glycol cleaning, specifically for filters used in polyester or PET applications, involves cleaning with glycol and processing the filters in a hot TEG installation. This technique breaks down polymers, removing contaminants. Any remaining contaminants can be removed through ultrasonic technologies.
Ultrasonic Cleaning
Ultrasonic cleaning is a fast, repeatable cleaning method. Filters are submerged in a suitable cleaning solution, using cavitation—microscopic bubbles implode, creating shock waves that produce a scrubbing effect on the filter surface. This ensures intensive but gentle removal of contaminants.
Thermal Cleaning
Thermal cleaning is used to remove larger contaminant deposits, such as specific polymers, in a pyrolysis oven. This process breaks materials down into smaller components that convert into gases and burn off at high temperatures or during the cracking process. This process takes around 12 hours but can be extended depending on contamination levels.
Low or High-Pressure Water Cleaning
This method is used with filters that need to be 100% grease-free, especially when used with O2 gases. This technique is safe for both people and the environment. Using an ultrasonic mobile unit, filters can be cleaned on-site, allowing critical components to remain in place, avoiding transportation-related damage.
Filter Inspection
After treatment, our quality manager performs a final inspection before returning the filters to you.
Testing Your Process Filters
Filters are tested upon receipt and after cleaning. When a filter is cleaned for the first time, this sets the baseline value. If test results show a significant difference from the baseline, the filter may be deemed unsuitable for reuse.
Testing options after cleaning include:
- Weight
- Bubble point in IPA
- Backflow in IPA
- Endoscope
- Microscope
- Material analysis
Bubble Point Test
In the bubble point test, pressure is applied to the filter to identify any perforations. Pressure is gradually increased until a bubble forms, known as the "bubble point value."
Backflow Test
In the backflow test, a constant air flow is applied to the filter, escaping through the membrane to visually assess filter permeability. If results fall below the minimum standard, the filter may be disqualified.
Weight
If the filter's weight is lower than the baseline, it may indicate damage to the filter material, while a higher weight suggests remaining contaminants.
Testing gives you assurance that you are reintegrating a complete, fully functional set of filters that meet the necessary process requirements. If any filters no longer perform to specifications, we will communicate this and can replace them with new filters.
We also offer a baseline test for new filters to ensure there are no leaks before use.
Filter Cleaning Reporting and Certification
We offer optional reports for filters that include certification according to:
- Quality Reporting ISO 9001
- Environmental Reporting ISO 14001
- Safety Reporting ISO 45001
Upon first receipt, you can request unique numbers to be engraved on filters for easy reference in our cloud application for previous inspections.
Cloud Application
Our cloud application tracks each cleaning’s performance results, giving you continuous insight into your filters' performance and alerting you when a filter truly needs replacement. This allows for replacing only those filters that no longer meet performance standards, instead of replacing all filters every cycle.
More Information on Filter Cleaning or a Custom TCO?
Would you like more information on filter cleaning, or are you curious if your filters are cleanable? We are happy to provide an overview of potential cost savings. Please feel free to contact me or one of my colleagues for a consultation.