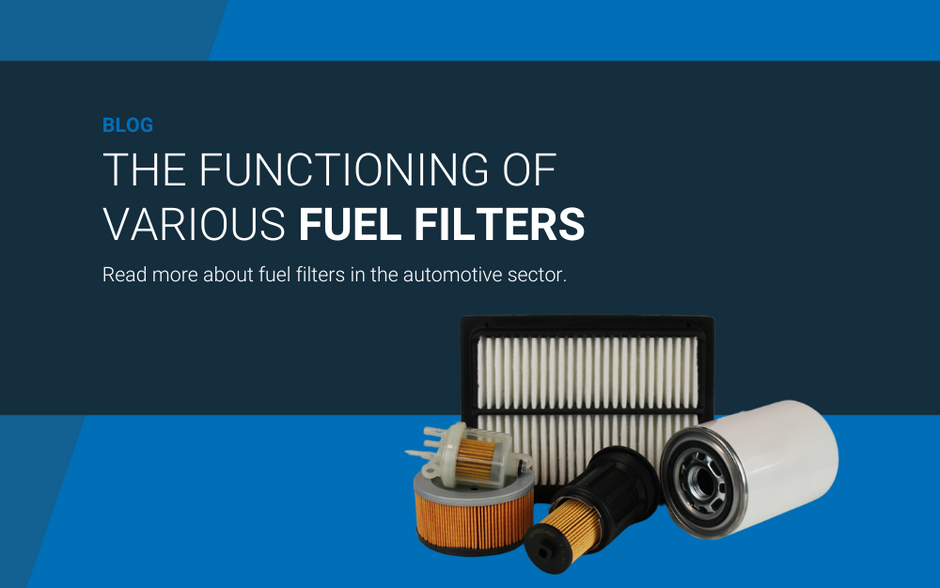
Fuel filters play an important role in maintaining the efficiency and reliability of engines in various industries, including shipping, offshore, and the automotive sector. In this blog, we discuss the importance of fuel filters, how they work, maintenance, why filters are essential for the optimal functioning of vehicles and machines in these industries, and what to look for when selecting the right fuel filters.
Why are fuel filters important?
Fuel filters are an essential component of the fuel system in engines. The filters are designed to remove contaminants such as dirt, water, and other particles from the fuel before it reaches the engine. Contaminants can reduce engine performance, cause wear on parts, and even lead to serious engine damage. Specifically, fuel pumps, carburetors, injection pumps, and injectors are sensitive to this. In hazardous industries where reliability and efficiency are very important, fuel filters play a crucial role in ensuring smooth operation and minimizing downtime.
Fuel filters prevent harmful substances from entering and damaging the engine, extending its lifespan and improving its efficiency. Using fuel filters reduces the risk of failures and accidents, improving the reliability and safety of the engines.
How do fuel filters work?
A fuel filter has a structure where the medium is cylindrical with a metal housing, including an inlet and outlet. The medium is typically made of high-quality cellulose fibers or even polyester.
Through the inlet opening, fuel enters from the main pump under high pressure, pushing the fuel through the medium. During this process, the medium filters out any impurities from the fuel, while the rest flows through and exits the filter via the outlet opening.
Some filters are equipped with a mechanism to remove water from the fuel, especially in diesel engines. Diesel filters typically feature a bowl at the bottom to collect the water removed from the fuel. This also has a drain valve to allow the water to be drained when needed, and a water sensor notifies the operator.
Fuel filters use physical filtration to remove various types of contaminants. Physical filtration removes larger particles like dirt and rust. In marine engines and offshore applications, fuel filters often have multiple filter elements to ensure thorough filtration due to challenging conditions and high demands.
Applications of fuel filters
Fuel filters have a wide range of applications across various sectors where they are essential for ensuring the reliability and performance of different types of engines. Fuel filters are used wherever a fuel combustion engine is employed. They are found in marine engines, offshore applications, vehicles in the automotive sector, and various industrial machines such as generators, pumps, and compressors.
What to consider when selecting fuel filters?
When selecting fuel filters for different applications, several key factors need to be considered. These include the type of contamination in the fuel, flow rate, filtration efficiency, the lifespan and ease of maintenance of the filters, and compatibility with the specific fuel type and engine manufacturer.
By considering these factors when selecting fuel filters, companies in shipping, offshore, and automotive industries can ensure they choose the right filtration solution that meets their needs and contributes to the reliability and efficiency of their vehicles and machines.
What types of fuel filters are there?
There are various types of fuel filters available, each designed to remove specific contaminants from the fuel and meet the requirements of different applications. Here are some common types of fuel filters:
Spin-on fuel filters are compact filters that are easy to install. They consist of a housing and a filter element that can be easily replaced when saturated. Spin-on filters are popular in the automotive sector due to their ease of use.
Water separators are specialized fuel filters designed to remove water from the fuel. Water in fuel can cause corrosion and reduce engine performance. These filters are especially important in maritime and offshore applications where water can enter fuel tanks.
Dual filter systems consist of two filters installed in series. The first filter removes larger contaminants, while the second filter removes finer particles. This ensures more thorough cleaning of the fuel and extends the lifespan of the filters.
Fuel separator filters are often used in heavy industrial applications and are designed to remove both solid contaminants and water from the fuel. They are robustly built and can handle large quantities of impurities.
In-line fuel filters are installed directly in the fuel line and are designed to remove contaminants from the fuel as it flows through the line. In-line filters are commonly found in both automotive and industrial applications.
Free advice on fuel filters
Would you like more information or advice on fuel filters? Feel free to contact me with any questions and for assistance with your situation. Contact via 0181 41 11 15 or via info@interfilter.nl.